De-Alcoholisation: A Detailed Look Into The Process
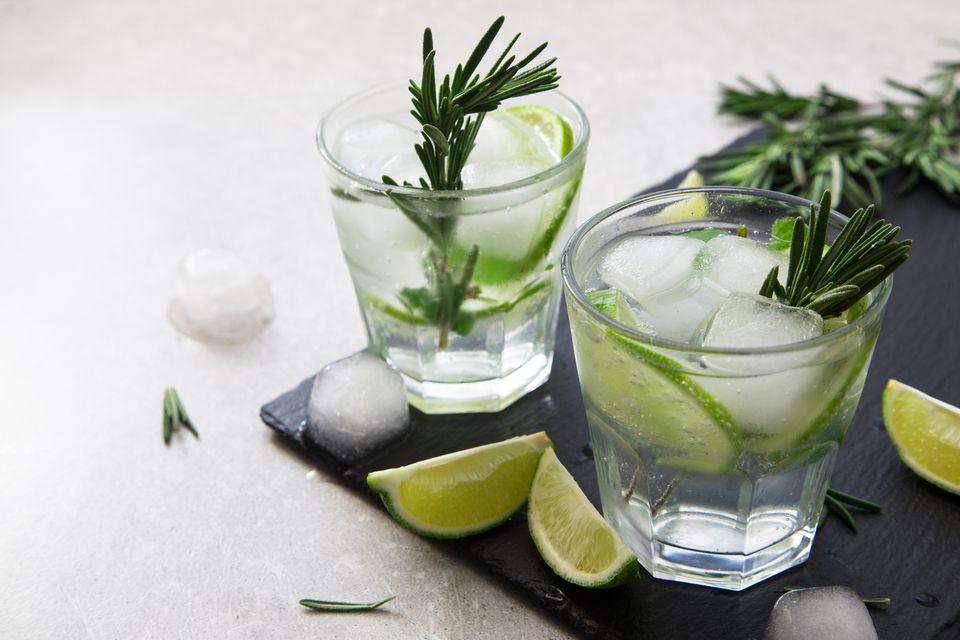
De-Alcoholisation: Reverse Osmosis Membrane Technology
De-Alcoholisation is a complex process and is heavily reliant on Reverse Osmosis. Reverse osmosis (RO) is a membrane-based technology that is used in diverse applications such as desalination, wastewater treatment, juice concentration, and de-alcoholisation (Wenten, 2016).
Reverse osmosis membranes use a smaller pore size compared to other pressure-driven membrane systems and allows for a more selective separation. This dictates that higher pressures are required for the process (Johnson and Nguyen, 2017).
The pressure used should be above the osmotic pressure of the solution in order to be separated. As a result, high pressure (up to 60 bar) is required in this operation. One of the biggest advantages of this system is the ability to retain temperature sensitive molecules (Catarino et al., 2007). In this technique, mostly asymmetric structures coupled with cellulose acetate, polyamide, and polyester sulfone layer membranes are used. (Alcantara et al., 2016).
De-Alcoholisation of Wine by Reverse Osmosis
In the past few decades, an increased market for low-alcohol and dealcoholized wine has developed. In addition, delaying harvesting to increase flavour content has resulted in grapes with elevated °Brix values, and corresponding wines with higher alcohol contents which can produce unbalanced wines. Conversely, delayed harvest, ostensibly to increase flavour potential, has resulted in wines with higher-than-typical alcohol content (Alston et al., 2011).
Previously, de-alcoholisation typically involved heat-induced alcohol evaporation. This method was successful, but it impacted on the flavour and odour of the final product. Correspondingly, this method was appropriate only for inexpensive, low-alcohol wines.
Vacuum distillation superseded this process as variables such as reducing the temperature in the process prevented flavours from being distorted. Unfortunately, this process on its own allowed important volatiles to escape along with the alcohol, which still impacted on the mixtures overall character and flavour.
Presently, the most widely used de-alcoholisation technique is a combination of vacuum distillation and reverse osmosis technology. (Fischer and Berger, 1996).
When alcoholic wines are treated to bring their alcohol content down to more traditional values, some flavour loss is typical and perceived to be a relatively minor factor industry wide. The alcohol content in the wine influences the bouquet, flavour and overall balance of the wine. Adjusting the alcohol content in the wine provides the winemaker with a unique opportunity to alter and adjust the wine’s characteristics.
Whenever the addition of water is deemed permissible or necessary in the production of low-alcohol beverages, dilution becomes the most straightforward way to obtain de-alcoholisation in the final mixture.
Reverse osmosis has developed greatly over the past thirty years and the costs associated with installing and commissioning a reverse osmosis plant have made them more accessible than ever. Until relatively recently, these procedures required expensive installations and extensive technical skill.
The application of these systems was strictly limited to very large wineries. Now, reverse osmosis operation is a more automated process and service contracts for these systems are obtainable though specialized firms such as Puretech Water Systems (UK) Ltd.
In addition to this, affordable benchtop units are becoming more readily available, which are appropriate for boutique wineries.
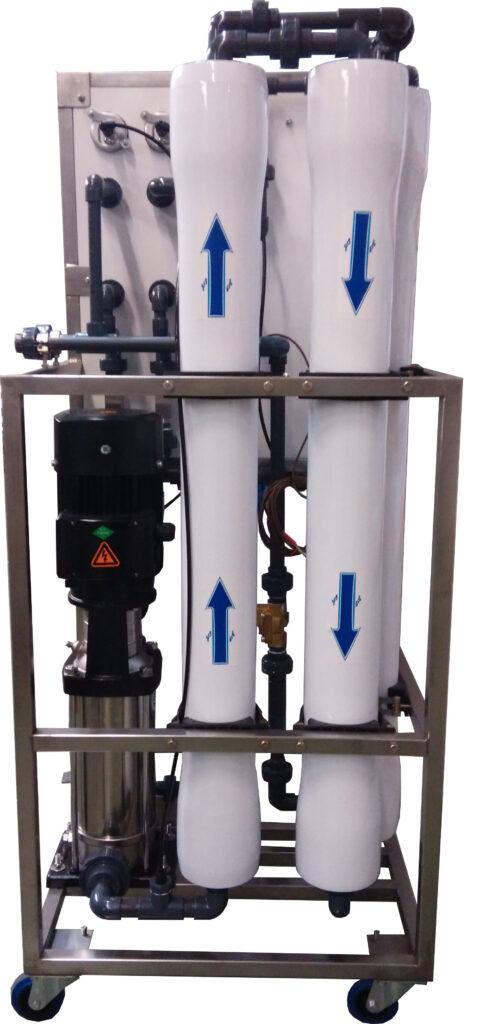
Removal Of Alcohol In Beer By Reverse Osmosis
Most beer contains approximately 90% water. The water quality that is used to brew the beer is of utmost importance. Here are two key factors of how water quality impacts on the final product:
- Water improves and intensifies the flavour and makes up majority of the mixture.
- Water is critical in the mashing process, and it can determine how efficient processes are.
Calcium, carbonate, chloride, magnesium, sulphate and sodium all impact upon the characteristics of the final product. The leading brewers and distillers use the highest available purity of water and then seek to add back some of these ions retrospectively.
Puretech Water Systems (UK) Ltd specialise in providing high-purity water for all brewers and can cater to all production volumes and varying requirements. We have experience working with micro-breweries and breweries alike.
In 2005, Catarino and colleagues studied the performance of the RO membrane for de-alcoholisation.
Different operating conditions and the ability of separation were investigated. In this technique, feed should overcome the osmosis pressure to move and permeate alcohol from a higher concentration stream to a lower concentration stream. The RO technique could remove alcohol from beer by using a semipermeable membrane without removing other compounds such as flavour compounds and aroma. It is common to operate a batch or semi batch mode. Desalination of pure water should continuously replace the water which is removed with alcohol. It is necessary to use a heat exchanger to keep the temperature constant (Catarino et al., 2006).
Feed pressure can lead to rejection and permeate flux of ethanol. Temperature increases lead to an increase of the permeate flow rate but an alcohol rejection decrease. Cellulose acetate performs the best in terms of alcohol rejection and permeate flux (Catarino et al., 2006).
Distilling & The De-Alcoholisation Of Spirits Using Reverse Osmosis
The well-established process of distilling spirits involves striking a fine balance between simple ingredients that create the character and complexity of the spirit. Water is the catalyst in this process and influences the final solution. It makes up majority of the solution as a key component and compounds the character and determines how the mixture combines.
The organic compound ethanol is the psychoactive agent in alcoholic beverages and can be made through the fermentation process with sugars and yeast. The fermentation process in creating liquors is only the beginning of the process, as the fermented product then requires distillation.
In some instances, traditional distillation and the ‘proof’ of an alcohol dictate whether it can be called a ‘gin’ or a ‘whiskey’. There are often legality issues surrounding what a product can be called because of this. Typically, anything under 37.5% ABV is not considered to be a gin for example. They are produced to look and taste as like their alcoholic counterparts with a very low or negligible alcohol content through de-acoholisation.
It is becoming more commonplace for distillers to distil these ‘low alcohol’ spirits and beverages using traditional distillation processes. Grain spirits which are perceived to be a plain alcohol, are added to a copper still. Often other botanicals are added to replicate the classic tastes and aromas associated with the liquor.
Once added to the still, the liquid is heated and the alcohol vapour which is created from heating purified water which has been produced by the reverse osmosis system, which then separates the alcohol. The vapour that is created is then cooled down and returns to a liquid state. This liquid is then further combined with pure water from the reverse osmosis system. Alcohol and water distil at different temperatures which results in ethanol and water-based distillations separating out easily.
Typically, when making standard strength alcoholic gin, the mixture is diluted by approximately half.
However, when making these ‘low alcohol’ version of the spirit the mixture is much more heavily diluted by the distiller with the pure water from the reverse osmosis system, which reduces the overall alcohol content by a much more significant margin until the desired alcohol to water ratio is achieved.
By distilling the mixture several times, the desired strength of the final solution can be achieved successfully. The base liquors that utilise the distillation process in this way are brandy, gin, rum, tequila, vodka and whiskey.
The Solution: Commercial Reverse Osmosis Systems
To properly treat water for brewing and distillation, it is important that all unnecessary contaminants are removed. Reverse osmosis is the most effective method for removing these contaminants. Chlorine and some organic materials are removed with a backwashing carbon filter to protect the reverse osmosis membrane and improve efficiencies.
If the water is over 70 mg/l of hardness (calcium and magnesium) then a water softener needs to be placed in front of the reverse osmosis system.
After the water is processed through the reverse osmosis system it is stored in an atmospheric storage tank in large volumes. In some instances, distilleries will opt to put RO water through a deionization (DI) system which results in what is commonly known as pure water with a pH of 7.0.
An ultraviolet (UV) light in-line is used to eliminate any bacteria when this water is feed to where it is next required. It is important to monitor the water quality from the reverse osmosis control panel to establish if certain consumables require replacing.
In certain instances, breweries will add calcium and other compounds back into the final mixture to alter the pH and mixture to taste.
In Distilleries it is commonplace for copper stills to be filled with a wash of a 50/50 mixture of neutral grain spirit and pure water. In addition to its use in the wash, pure water produced by the reverse osmosis system is also used for diluting the final mixture to bottling strength, somewhere typically in the region of 37.5% – 60% ABV.
Find Out More
We manufacture and stock a wide range of plants for brewing and distilling processes that can meet exacting flow rate requirements for de-alcoholisation.
As an example, our larger units can supply over 50,000 litres per day. We pride ourselves on our bespoke configurations that are tailored to meet the requirements of each of the industries that we work with.
Here’s more about how the adaptive design works:
- All of our plants come with 3 flow meters.
- Stainless Steel Frames
- Microfiltration at 5 microns
- TDS Elimination up to 99.2%
Puretech Water Systems (UK) Ltd are a leading water treatment plant manufacturer. We are leading Commercial Water Softener Plant manufacturers and Commercial Reverse Osmosis Plant manufacturers.
We provide a 1st class installation and maintenance services on our own equipment as well as other manufacturers equipment. Our industry expertise and customer focused approach provide you with the best customer support possible and the service your company deserves.
Contact us to find out which Commercial Reverse Osmosis Unit best suits your application.
Call us to consult with an expert today! For a competitive quotation, call 01622 871 877.
More Articles
- All
- News